THE EFFECTIVENESS TEST RESULTS
Our tests showed clearly that the most effective method of clearing blocked channels of DPF / FAP / KAT filters is to clean them with a water jet under high pressure with a well chosen detergent.
On the other hand, the worst and the most invasive method turned out to be chemical treatment.
Hydrodynamic treatment as the only one gave a chance to remove all types of particulates, both from inlet and outlet channels of the filter insert. World HYDRO FLUSH has proven that precision-controlled water jet cleaning combined with optimized detergents ensures both deep cleansing and maximum filter safety.
The working fluid jet in the machine is directed from the outlet side of the filter, that is from usually unobstructed outlet channels, and then water with the detergent gets into micropores in the walls separating the channels to blocked inlet channels.
The filter is fastened vertically in the machine, with the outlet side from the top (where the water jet is applied).
Such a position of the filter enables free cleaning of inlet channels of the filter, which in this position have the channels opened at the bottom, where the contaminated water with all deposits can freely get outside the filter.
The other methods did not guarantee such effectiveness with the simultaneous maintenance of safety for the filter insert.
Heat treatment in the induction furnace enables curing soot in the filter channels to the form of ash, so differently than it takes place in the exhaust system where soot particles react with nitrogen dioxide from exhaust fumes, out of which carbon monoxide and nitrogen oxide form. They combine with oxygen forming carbon dioxides and nitrogen dioxides getting out from the system through outlet channels.
To put it simply, soot oxidizes there to the gaseous form which finds it much simpler to get out of the filter than ash.
Moreover, the effectiveness of this method depends a bit on luck.
Too short time for the treatment is the reason for which highly compressed soot inside the filter core is not burnt and the filter will not obtain full effectiveness. On the other hand, too long heating time leads to the degradation of the filter core. After heat treatment the filter insert channels are blocked with ash which, depending on the previous process of soot curing, it is more or less suitable for blowing with compressed air.
Ultrasonic treatment copes only with little or mildly dirty filters.
Unfortunately, the majority of filters are given to be cleaned when they are very contaminated.
In such filters, water with ultrasounds does not reach all corners, leaving some channels blocked. In this method also final blowing with compressed air is needed, which with various degree of success removes dissolved deposits from the filter insert channels.
Pneumatic treatment is not really able to clean filters contaminated with oil and with cured carbon deposits.
It is not rare. The failure of the supercharger, injection often lead to flooding the DPF filter with oil.
In addition, it is necessary in this method to cut the filter, remove the filter core and weld it afterwards.
Curing in the service mode has sense in cars with really low mileage where in blocked channels clean soot prevails. It is easy to cure such soot to the gaseous form.
In cars with the mileage above 100,000 km, such a treatment rarely turns out to be effective.
Cured soot frees only a small part of the filter channels, the remaining part is still blocked with ash.
Cleaning with chemicals is a real torture for the filter insert.
In the majority of cases the chemical substance dissolves and combines with the filter particulates, blocking it even more. In many cases the filter insert becomes damaged mechanically.
Owing to the experience gained, we chose the method of cleaning with water jet under high pressure.
In the first phase we focused on the elimination of potential flaws, namely: ill-chosen detergent, or too high power of the compressed air in the fluid working jet.
In order to meet the challenge we developed our own detergent and cleaning machines.
In consequence of the undertaken activities, our authorial technology has been created.
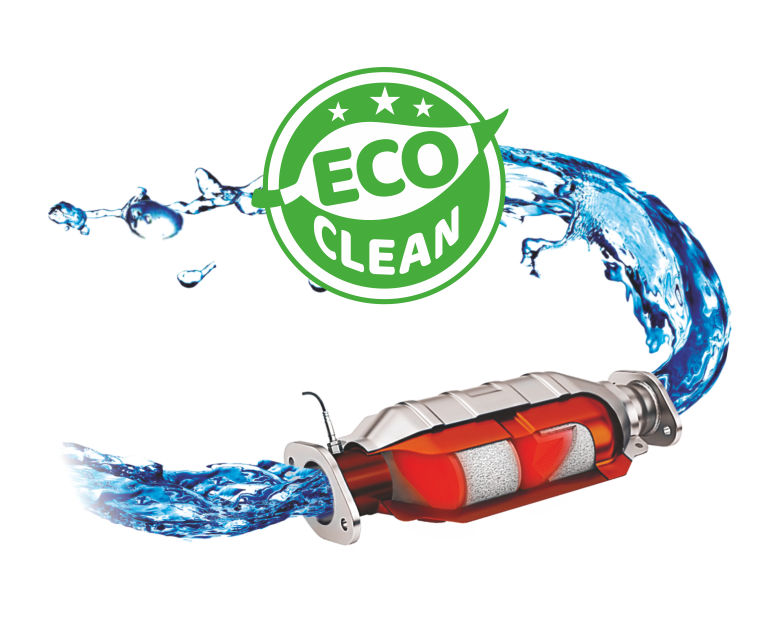

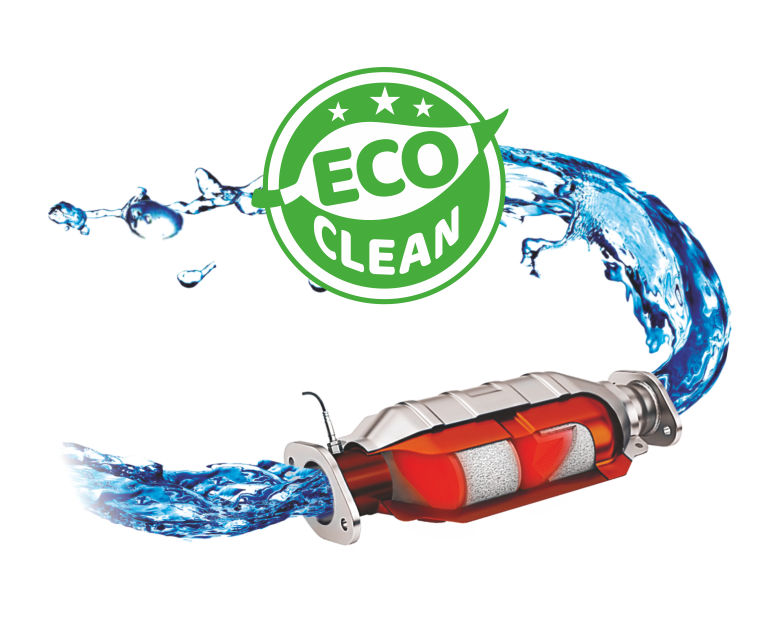